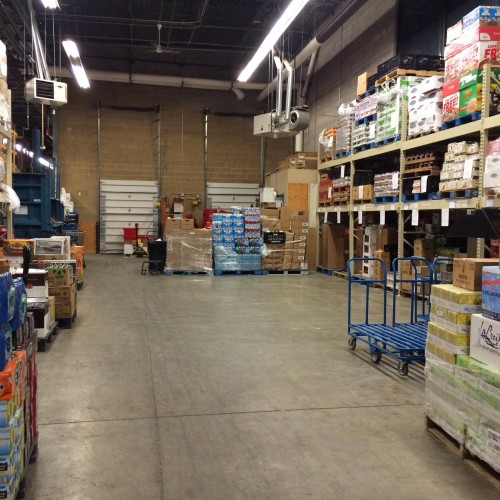
posted 4th May 2025
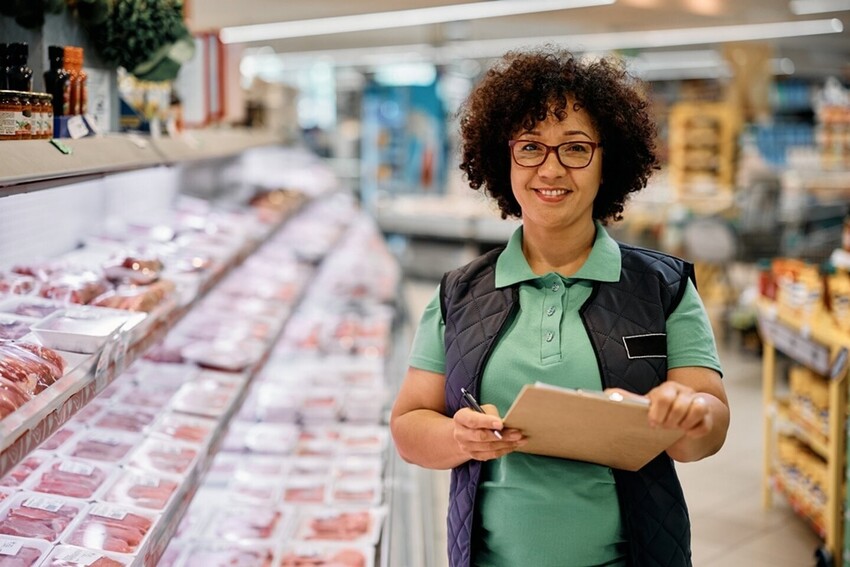
While customer-facing operations typically receive the lion's share of attention and resources in retail and hospitality businesses, the backroom represents the beating heart that powers the entire enterprise. This often-overlooked space serves as command central for inventory management, order fulfillment, staff coordination, and countless operational functions essential to business success. When backroom operations falter, the ripple effects quickly reach customers through stockouts, delays, pricing errors, and diminished service quality. Conversely, optimized backroom operations create a foundation for exceptional customer experiences through seamless product availability, accurate pricing, and responsive service delivery.
The backroom landscape has transformed dramatically in recent years through technological innovation, process refinement, and evolving management philosophies. Modern backroom operations bear little resemblance to their predecessors, embracing automation, data analytics, and specialized expertise to maximize efficiency while minimizing error rates. This evolution represents more than mere modernization it demonstrates a fundamental shift in how businesses conceptualize their operational nerve centers and the resources required to maintain peak performance across increasingly complex supply chains and customer expectations.
Control through Professional Stocktaking Services
Traditional inventory management approaches relied heavily on seasonal counting events that provided only periodic glimpses into inventory reality, leaving significant blind spots between counts. These antiquated methods frequently resulted in compounding errors, shrinkage mysteries, and stock discrepancies that undermined operational confidence and financial accuracy. Contemporary inventory management has evolved dramatically through specialized stocktaking services that transform counting from disruptive events into ongoing processes integrated seamlessly into regular operations without business interruption.
Professional stocktaking specialists employ sophisticated methodologies that extend far beyond simple counting to include variance analysis, trend identification, and shrinkage pattern recognition that address root causes rather than merely documenting discrepancies. These services typically utilize advanced scanning technologies, cloud-based verification systems, and statistical sampling techniques that achieve near-perfect accuracy while requiring only fraction of the time and labor demanded by traditional approaches. The resulting inventory precision supports confident purchasing decisions, optimal stock levels, and financial reporting accuracy that traditional periodic counting methods simply cannot match in today's fast-moving inventory environments.
Workspace Organization
The physical arrangement of backroom spaces profoundly influences both operational efficiency and employee satisfaction in ways that extend far beyond simple convenience. Cognitive scientists studying workplace environments have documented how space configuration directly impacts cognitive load, decision fatigue, error rates, and job satisfaction across various operational settings. Well-designed backrooms incorporate psychological principles that minimize unnecessary mental processing while maximizing attention for critical tasks requiring precision and judgment.
Effective backroom layouts create intuitive work flows that align with natural cognitive patterns, reducing the mental effort required for routine operations. This cognitive efficiency becomes particularly critical during peak demand periods when decision speed and accuracy face simultaneous pressure. Elements as seemingly minor as lighting quality; noise levels, and color coding schemes significantly impact information processing speeds and error rates, particularly for tasks requiring sustained attention or complex decision sequences. When these psychological factors receive proper consideration in backroom design, both operational metrics and employee retention typically show measurable improvement compared to spaces designed solely for physical efficiency.
Technological Integration without Disruption
Technology implementation in backroom operations frequently creates temporary performance declines as staff adapt to new systems and workflows a phenomenon that sometimes undermines otherwise promising innovations. This implementation dip represents a significant barrier to operational advancement, particularly for businesses operating with minimal margins or during peak seasons when performance continuity remains essential. Successful implementation approaches have evolved to address this challenge through phased deployments, targeted training protocols, and hybrid periods that maintain critical functions through parallel systems during transitions.
Modern implementation methodologies emphasize extensive pre-deployment simulation rather than on-the-job learning, allowing staff to develop system familiarity before facing real-world consequences for errors. These approaches typically create custom training scenarios reflecting actual operational conditions rather than generic tutorials, significantly reducing adaptation periods and associated performance declines. The most successful technology integrations maintain continuous feedback loops during implementation, identifying and addressing friction points in real-time rather than waiting for scheduled evaluation periods when problematic patterns may have already become entrenched.
Staff Empowerment with Cross-Functional Expertise
Traditional backroom staffing models frequently created rigid functional silos that limited operational flexibility and response capability during fluctuating demand periods or unexpected disruptions. Contemporary approaches increasingly emphasize cross-functional training that enables team members to operate effectively across multiple operational domains rather than specializing narrowly in isolated functions. This versatility creates substantial advantages in scheduling efficiency, disruption response, and career development opportunities that benefit both operations and individual team members.
Cross-functional training programs systematically rotate staff through various operational areas with progressive responsibility levels, developing practical expertise rather than theoretical knowledge. These approaches typically incorporate mentorship components pairing experienced specialists with developing team members to transfer tacit knowledge that formal training often fails to capture. The resulting workforce flexibility allows operations to rapidly reallocate resources toward pressure points as they emerge, maintaining performance levels during unexpected challenges while reducing dependence on specific individuals for critical functions—a significant resilience factor for operations of all sizes.
Minimizing Shrinkage through Environmental Design
Inventory shrinkage represents a persistent challenge across retail and hospitality operations, with combined external and internal losses significantly impacting profitability despite ongoing prevention efforts. Traditional approaches emphasized security measures that sometimes created adversarial workplace dynamics while achieving only modest results. Environmental design approaches have emerged as more effective alternatives that reduce theft opportunities through subtle space modifications rather than overt security measures that can damage workplace culture and trust.
Effective environmental design incorporates natural visibility principles that eliminate concealed areas where unauthorized activities might occur unobserved. These approaches strategically position high-value inventory in naturally monitored zones while creating workflow patterns that provide informal observation without explicit surveillance. Physical elements like strategic mirror placement, appropriate lighting levels, and transparent storage solutions create environments where privacy for inappropriate activities simply doesn't exist without explicitly communicating distrust. When combined with positive culture-building initiatives that emphasize organizational citizenship, these environmental approaches typically reduce shrinkage more effectively than traditional security-focused measures.
Dynamic Scheduling for Operational Resilience
Traditional scheduling approaches emphasized consistency and predictability over responsiveness, creating rigid structures those frequently misaligned staffing resources with actual operational needs. Contemporary scheduling systems have evolved dramatically, utilizing predictive analytics to anticipate demand fluctuations and automatically adjust staffing recommendations based on multiple variables including historical patterns, weather forecasts, promotional activities, and seasonal factors. This dynamic approach significantly improves labor efficiency while enhancing service levels during peak periods.
Advanced scheduling systems incorporate employee preference data alongside operational requirements, balancing business needs with quality-of-life considerations that significantly impact retention rates. These systems typically offer limited self-scheduling options within operational parameters, creating greater work-life balance without compromising coverage for critical periods. The resulting schedules achieve superior alignment between staffing levels and actual requirements while reducing the administrative burden associated with frequent manual adjustments to address changing conditions or employee availability changes.
Continuous Improvement through Systematic Feedback
Meaningful operational improvement requires systematic feedback mechanisms that capture performance data, identify improvement opportunities, and track progress toward specific objectives. Traditional approaches relied heavily on management observation and periodic reviews that provided limited visibility into daily operational realities and improvement possibilities. Contemporary operations increasingly implement structured feedback systems that generate continuous improvement insights from multiple sources including performance metrics, customer feedback, employee observations, and competitive benchmarking.
Effective feedback systems emphasize solution identification rather than problem cataloging, encouraging participants to propose specific improvement approaches alongside issue identification. These systems typically incorporate rapid experimentation protocols that allow small-scale testing of promising ideas before full implementation, reducing the risk associated with operational changes while accelerating innovation cycles. According to research from the International Journal of Production Economics, organizations implementing structured continuous improvement feedback systems achieve approximately 37% higher performance gains compared to traditional periodic review approaches over equivalent time periods.
Sustainability Integration in Backroom Operations
Backroom operations create significant environmental impacts through energy consumption, waste generation, material handling processes, and procurement decisions that traditionally received limited scrutiny from sustainability perspectives. Contemporary operations increasingly incorporate environmental considerations into standard procedures, recognizing both the ethical imperative and potential cost savings associated with more sustainable approaches. These initiatives typically focus on energy efficiency, waste reduction, sustainable packaging, and optimized transportation logistics that reduce environmental impact while simultaneously improving operational efficiency.
Modern sustainability approaches emphasize measurement and quantification rather than general intentions, establishing specific baseline metrics and improvement targets for key environmental indicators. These systems typically incorporate regular sustainability audits that identify improvement opportunities through systematic evaluation rather than incidental observation. The resulting operational adjustments frequently deliver meaningful cost reductions alongside environmental benefits, particularly in energy consumption, waste management, and transportation efficiency where economic and environmental interests naturally align despite common misconceptions about sustainability requiring financial sacrifices.
Closing Thoughts
The evolution of backroom operations from necessary cost centers into strategic assets represents one of the most significant yet underappreciated business developments in recent decades. This transformation reflects deeper recognition that operational excellence doesn't merely support business strategy it fundamentally enables capabilities that would otherwise remain theoretical despite the best customer-facing initiatives. As competitive pressures continue intensifying across sectors, the distinction between market leaders and followers increasingly depends on backroom operational capabilities that remain invisible to customers yet powerfully determine the experiences those customers ultimately receive.
The most profound aspect of this transformation extends beyond specific technological implementations or management techniques into fundamental perspective shifts regarding backroom operations. Contemporary approaches recognize these spaces not as secondary support functions but as primary value creation centers that directly enable competitive advantages through capabilities competitors cannot easily replicate. This philosophical reframing drives investment decisions, talent acquisition strategies, and organizational priorities that collectively elevate backroom operations from necessary infrastructure into strategic differentiators capable of defining market positions. In this evolution, we witness the future of operational excellence—one where backroom functions receive attention, resources, and recognition proportionate to their true business impact rather than their customer visibility.