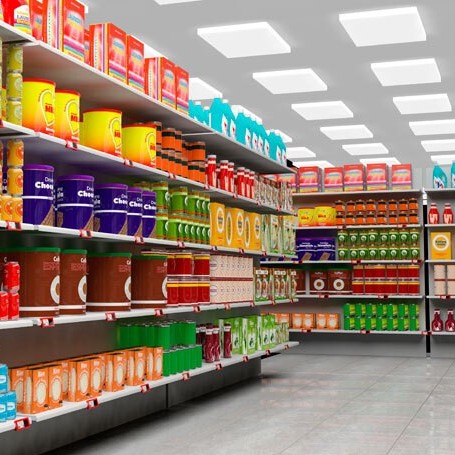
posted 5th May 2025
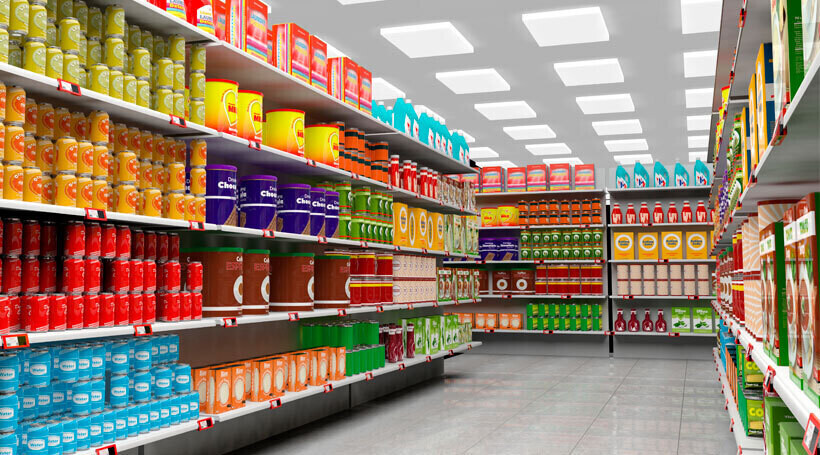
Every item that vanishes without generating revenue carves away at profitability with silent efficiency. This phenomenon product shrinkage represents the gap between inventory that should exist and what actually remains available for sale. In retail environments alone, this invisible drain siphons billions annually from bottom lines worldwide. Yet many organizations continue treating shrinkage as inevitable background noise rather than a controllable variable. This resignation stems less from actual immutability than from fragmented understanding of shrinkage's multidimensional causes and solutions. By reconceptualizing product disappearance as a systemic challenge rather than isolated incidents, businesses can dramatically reduce these losses through coordinated intervention.
Numbers That Whisper Truth
Regular stock counting reveals patterns typically invisible through day-to-day observation. These systematic inventory audits expose not just quantities but crucial timing and location signatures that point toward specific causes. Without this quantitative foundation, shrinkage reduction efforts operate essentially blind, addressing symptoms rather than root causes. The metrics generated through consistent counting create the diagnostic framework necessary for effective intervention.
Frequency transforms ordinary inventory checks into powerful analytical tools. When businesses increase counting cadence from quarterly to monthly or even weekly for high-risk categories, entirely new patterns emerge. Sudden accelerations in loss rates frequently correlate with specific operational changes, staffing adjustments, or procedural modifications previously considered unrelated to inventory control. These temporal relationships remain undetectable without sufficient measurement density.
Location-specific analytics provide equally valuable insights. Comparative analysis across similar store formats often reveals dramatic shrinkage variations despite seemingly identical operations. These disparities typically indicate either exceptional performance worth replicating or problematic execution requiring intervention. Neither conclusion becomes possible without location-tagged inventory data gathered through disciplined counting protocols.
Product category analysis adds another crucial diagnostic dimension. Most businesses discover that shrinkage concentrates disproportionately within specific merchandise categories rather than distributing evenly across inventory. These patterns often contradict intuitive assumptions about which items disappear most frequently. High-value products under enhanced security measures sometimes experience lower shrinkage rates than seemingly low-risk items that receive minimal protection precisely because of their perceived unattractiveness to thieves.
Environmental Architecture
Physical environments silently shape behavior through subtle cues that either discourage or inadvertently encourage product diversion. Progressive businesses recognize these spaces as malleable canvases for loss prevention rather than fixed constraints. Through deliberate environmental reconfiguration, they create settings where theft requires significantly more effort while legitimate access remains frictionless.
Sightline engineering represents one powerful environmental intervention. When store layouts eliminate blind spots and create clear visibility throughout merchandise areas, opportunistic theft becomes substantially more difficult. This approach extends beyond simple camera placement to fundamental design decisions about fixture height, aisle configuration, and product positioning. Effective implementations maintain aesthetic appeal while eliminating concealed areas where products might be consumed, concealed, or repackaged.
Transition zone management addresses vulnerability periods when products move between secured areas. Loading docks, delivery entrances, and storage access points create natural bottlenecks where accountability can be either reinforced or compromised. Forward-thinking businesses apply enhanced procedural controls specifically at these junctures, recognizing them as disproportionately vulnerable to both internal and external shrinkage.
Product adjacency strategies reduce theft by strategically positioning high-risk items near natural surveillance points. Rather than clustering valuable merchandise in easily targeted sections, this approach distributes these products near staff workstations, customer service areas, or other locations with consistent employee presence. The resulting environmental design maintains sales potential while significantly increasing risk perception for potential thieves.
Fixture design itself contributes significantly to shrinkage prevention. Modern manufacturers offer merchandise display systems incorporating subtle security features without projecting institutional aesthetics. Locking showcases that maintain visual appeal, sensormatic-integrated shelving, and product-specific security fixtures create physical barriers while preserving customer experience quality. These solutions address the critical challenge of protecting merchandise without creating shopping environments that feel unwelcoming or suspicion-oriented.
Procedural Discipline
Written policies mean little without consistent execution throughout organizational hierarchies. Effective shrinkage reduction requires procedural discipline that transforms theoretical protection into daily practice. This consistency depends less on policy sophistication than implementation thoroughness even simple measures applied universally outperform elaborate controls deployed sporadically.
Receiving protocols represent critical control points where accuracy directly impacts shrinkage metrics. When businesses implement verification requirements including blind counts, random audits, and delivery driver retention until completion, they create accountability impossible under cursory check-in procedures. These protocols detect both intentional diversion and honest delivery errors that would otherwise translate directly to inventory discrepancies.
Transfer documentation requirements address internal movement vulnerability. Products traveling between locations, departments, or storage areas create natural accountability gaps when movements occur without rigorous documentation. Implementing transfer verification processes where both sending and receiving parties independently confirm quantities eliminates the phantom shrinkage that occurs when items simply disappear into procedural cracks.
Return processing disciplines prevent shrinkage through improper credit issuance. Without structured verification procedures, return counters become potential profit leak points where employees can process fraudulent returns or manipulate transactions to facilitate theft. Properly designed return procedures include product condition verification, receipt validation, and transaction pattern monitoring to identify suspicious activity requiring additional scrutiny.
Destruction documentation completes the product lifecycle control framework. Items damaged, expired, or otherwise unsellable must follow documented disposal processes with supervisor verification to prevent functional products from disappearing through falsified damage claims. This seemingly minor control point addresses a common shrinkage vector where saleable merchandise exits through backdoors disguised as legitimate waste.
Technology Integration
Modern loss prevention technologies provide powerful tools that simultaneously increase protection effectiveness while reducing labor requirements. However, technology alone rarely solves shrinkage challenges without corresponding procedural integration. Successful implementations treat technological solutions as force multipliers for human oversight rather than replacements for fundamental controls.
Exception-based reporting systems transform overwhelming data streams into actionable intelligence. These platforms apply algorithmic analysis to transaction patterns, identifying statistical outliers requiring investigation. The resulting alerts direct limited loss prevention resources precisely where anomalies suggest potential issues rather than diluting effort across universal monitoring. This targeted approach dramatically increases intervention effectiveness while minimizing operational disruption.
RFID evolution has transformed inventory tracking capabilities where implementation proves financially viable. Modern systems provide near-real-time visibility to inventory location, enabling immediate alerting when products move into unauthorized areas. These capabilities extend traditional EAS approaches by providing specific item identification rather than simply detecting tag presence. The resulting granular visibility creates accountability previously impossible with conventional tracking systems.
Video analytics capabilities now extend far beyond passive recording to active monitoring. Advanced systems can detect specific behavioral patterns associated with theft preparation, alert security personnel to suspicious activity, and create evidentiary records for subsequent investigation. These capabilities transform surveillance from reactive documentation to proactive intervention, potentially preventing losses before they occur.
Biometric access controls address internal shrinkage by creating non-transferable authentication requirements for restricted areas or operations. Unlike keys or access cards that can be shared among individuals, fingerprint, retinal, or facial recognition systems create individualized accountability trails whenever sensitive inventory areas are accessed. This technology eliminates anonymous entry one of the primary enablers of internal product diversion.
Employee Investment
Workforce engagement represents perhaps the most underutilized shrinkage prevention resource. When employees personally invest in inventory protection, they create a human surveillance network far more perceptive than any technological system. Developing this cultural alignment requires specific strategies that transform loss prevention from abstract corporate concern to personal priority.
Incentive alignment creates tangible connections between shrinkage performance and employee benefits. Bonus structures incorporating inventory variance metrics, team celebrations for shrinkage reduction achievements, and recognition programs for proactive prevention efforts all demonstrate organizational seriousness while providing personal motivation. These programs transform employees from passive observers to active participants in protection efforts.
Transparency about financial impact helps employees understand shrinkage consequences beyond abstract percentage targets. When staff comprehend how inventory loss directly affects resources available for wages, benefits, and working condition improvements, they develop personal stake in prevention efforts. This understanding transforms abstract corporate losses into concrete personal impacts that motivate protective behavior.
Anonymous reporting mechanisms address the social barriers that often prevent employees from sharing shrinkage observations. Well-designed programs provide confidential channels for communicating concerns without fear of retaliation from peers or supervisors potentially involved in improper activities. These systems capture valuable intelligence that would otherwise remain suppressed by social pressure against "informing" on colleagues.
Comprehensive training programs ensure employees recognize both obvious and subtle shrinkage indicators. Beyond identifying blatant theft attempts, staff learns to spot procedural weaknesses, suspicious patterns, and operational vulnerabilities that might facilitate inventory loss. This educational investment transforms the entire workforce into a distributed detection network operating throughout business hours.
Leadership Visibility
Executive engagement directly influences organizational shrinkage performance through both symbolic and practical channels. When leadership demonstrates genuine commitment to inventory protection through visible actions rather than mere policy statements, they establish cultural expectations that permeate operational levels. This commitment manifests through specific behaviors that signal priority status.
Regular shrinkage discussion in management meetings establishes issue prominence. When inventory variance receives agenda time alongside traditional financial metrics, the organization demonstrates serious commitment to reduction efforts. This visibility ensures middle management prioritizes prevention rather than treating it as secondary concern behind sales or operational targets.
Cross-functional accountability prevents the common problem of departmentalized responsibility where shrinkage becomes exclusively "loss prevention's problem" rather than organization-wide priority. Effective structures incorporate shrinkage metrics into performance evaluations across departments including operations, merchandising, receiving, and sales—recognizing that vulnerability exists throughout the product lifecycle rather than at isolated points.
Resource allocation provides the ultimate demonstration of genuine priority. Organizations truly committed to shrinkage reduction invest accordingly, providing necessary funding for technology implementation, procedural development, training programs, and adequate staffing. These investments signal that inventory protection represents genuine priority rather than merely rhetorical concern.
Leadership presence in prevention activities reinforces programmatic importance. When executives participate in inventory counts, randomly verify receiving procedures, or engage directly with loss prevention initiatives, they demonstrate commitment beyond delegation. This visible involvement creates implementation energy impossible to generate through policy directives alone.
Ending Notes: Systemic Approach to Vanishing Margins
Product shrinkage represents a complex challenge requiring multidimensional response rather than isolated tactics. Organizations achieving exceptional results recognize that sustainable reduction comes through coordinated efforts across environmental design, procedural discipline, technological leverage, cultural alignment, and leadership engagement. This systems thinking transforms shrinkage from mysterious disappearance to manageable variable.
The financial implications extend far beyond the direct value of missing merchandise. In retail environments with typically thin margins, each percentage point of shrinkage reduction flows directly to bottom-line profitability with multiplier effects exceeding most other performance improvements. This leverage explains why market-leading organizations increasingly view shrinkage control as strategic priority rather than operational nuisance.
As competitive pressures continue compressing margins across industries, inventory protection becomes increasingly critical to financial sustainability. Organizations implementing comprehensive approaches position themselves for significant competitive advantage through preserved margins their less-disciplined competitors surrender to shrinkage. This performance gap widens over time as protection capabilities compound through iterative improvement while shrinkage costs similarly accumulate for those failing to address this silent profit drain.